Altair Inspire Extrude 2023.0 Win x64
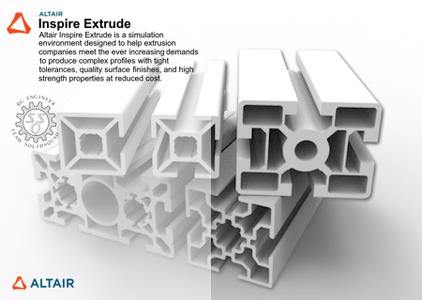
Free Download Altair Inspire Extrude 2023.0 | 3.7 Gb
Owner:Altair
Product Name:Inspire Extrude
Version:2023.0
Supported Architectures:x64
Website Home Page :www.altair.com
Languages Supported:english
System Requirements:Windows *
Size:3.7 Gb
The Altair Engineering development team is pleased to announce the availability ofAltair Inspire Extrude 2023.0is an easy-to-use tool for simulating metal extrusion, polymer extrusion, and friction stir welding processes to detect potential defects early in the product development phase and improve the process efficiency.
The Inspire Extrude 2023 release includes the following new features and enhancements.
General
Custom Icon Ribbons
In this release, the user can create custom icon ribbons. Any icon from another existing ribbon can be copied to the custom ribbon using simple drag and drop. These ribbons will be remembered in the application and will be available when the application is invoked again.
Advanced Tooltips
Advanced tooltips are now enabled for all Inspire Extrude tools. This will give the user a quick idea about the functionality of the tool. (IEXT-3137).
Metal Extrusion
Create Dies for Solid Tube Extrusion
In this release, die creation tools are implemented in Inspire Extrude Metal. Users can create Conical or Flat Dies for solid tube extrusion. The interface takes very few parameters and constructs the preferred Die part. The part also is oriented appropriately as per the Extrusion axis. This feature is built using the construction history which is a powerful tool in Inspire. (IEXT-3155, IEXT-3037).
Bearing Start Curve
The metal extrusion solver supports the non-uniform start of the bearing region in the model. This feature considers a non-uniform bearing start before the start of the BEARING3D region (in the tet4-meshed zone), and this enables analysis of more complex dies with such bearing regions. Starting with this release, the interface will support this feature, and this is implemented via a bearing start curve. Users can manually extract this curve, and it must be named in accordance with the end curve. (IEXT-3017)
Control Biased Meshing of Bearing and Profile
In this release, biasing parameters for Bearing and Profile regions can be specified in the Export dialog. Varying the Biasing Intensity and the Number of Layers shows the estimated first and last layer size for Bearing. Using these inputs, the interface computes and adjusts the biasing intensity and number of layers on Profile automatically. (IEXT-2952)
Mandrel Mesh Factor
In previous releases, the mesh factor was enabled through a system environment variable. Now this is available in the user interface, and users can specify this value in the Export Dialog. Using this factor, the mesh on the load surfaces of Mandrel will be refined. (IEXT-2833)
Extrusion Ratio and Profile Speed
Export Dialog will now show the computed Extrusion ratio and Profile Speed data. These values are auto-computed based on model geometry and the ram speed input. (IEXT-3193)
User-Defined Functions (UDF) for Materials and Grain Size
In this release, the interface will support the specifying UDF loaded as a shared library object (DLL/so). These UDF are written in C (preferred) or Fortran programming languages and compiled using the free Intel One API compiler. In Linux platforms, the GCC compiler is also supported. On selecting the DLL, the functions in that shared object will automatically be listed as a combo box, and the preferred function can be selected. (IEXT-2815).
Improvements to Strain Prediction
Strain should be zero on the walls with no-slip condition and non-moving contact BC. The solver was enforcing only the values at the inlet, and the numerical solution was expected to naturally capture the dead zone and zero strain on the tool contact surface. This issue is resolved now, and this will lead to much more reasonable values of strain without hot spots, and the dead zones will be captured more accurately. (HXT-253, HXT-278, HXT-668)
Tool Deflection
Reference Temperature and Thermal Stresses
Thermal stresses arise due to non-uniform temperature distribution, and it is computed with reference to the temperature specified in TEMP(INIT) or MATx TREF cards in the OptiStruct deck. Not specifying this correctly will lead to errors in the computed stresses. This data is not needed for a two-step analysis where the first step is a heat transfer analysis that accurately computes this. But, it is needed for the standard tool stress analysis which uses the load from extrusion and assumed temperature.
In this release, users will be able to specify the reference temperature of each tool part and, more importantly, they will be able to disable the use of thermal stresses. To specify the temperature of tool parts, a new temperature icon/interface is added. When thermal stresses are ignored, only the extrusion stress loads will be used to compute the deformation. (IEXT-3167)
Unit System Mismatch in Imported HMASCII Files
Inspire Extrude is unit-friendly and enables the customer to use the unit system of their choice. This flexibility requires the data to be consistent, especially when using previously computed loads on tool-workpiece contact surfaces via the HMASCII file. Any inconsistency and mismatch of the units will lead to preprocessing issues and erroneous results.
Inspire Extrude will now issue a warning message if the units used in the extrusion analysis and the loads in the imported HMASCII files are not consistent. The requirement is that the HMASCII file should contain the unit system information. (IEXT-2900)
Loads on Relief Regions Due to Mapping Errors
In a coupled analysis, extrusion loads on the tool-workpiece contact surfaces are used in the tool stress analysis. Now, the interface will exclude these regions using the bearing curve data, and they will not incorrectly affect the analysis. (IEXT-3195)
Quenching
Specification and Visualization of Boiling Heat Flux Curve
The boiling heat flux curve is used in immersion quenching analysis, and now users will be able to specify the data that defines this curve and also visualize it. This data will be exported to the solver deck and used in the analysis. (IEXT-3010)
User-Defined Functions (UDF) for Grain Size and Heat Transfer Coefficient (HTC)
In this release, the interface will support the specifying UDF loaded as a shared library object (DLL/so). These UDF are written in C (preferred) or Fortran programming languages and compiled using the free Intel One API compiler. In Linux platforms, the GCC compiler is also supported. On selecting the DLL, the functions in that shared object will automatically be listed as a combo-box and the preferred function can be selected. (IEXT-2815).
Quenching Results are Written only after Profile Exits Die
The model setup for quenching requires the entire profile length to be meshed, however, the results computed are relevant only for the extruded portion of the profile at any given time. The solver is now enhanced to write the results only for this portion and not write the initial data for the non-extruded section, which is a numerical artifact. To support this, a new parameter named DieAssemblyExitLocation is added to the solver. (HXT-640)
Improved Quenching Warpage Analysis
The elastic residual stress is computed for the elements that have exited the die and accounted for the warpage computation, with an aim to improve the warpage prediction. For this purpose, a new warpage analysis type "ElasticResidual" is introduced. This can be set using the parameter WarpageAnalysisType. (HXT-598)
Polymer Extrusion
Import Materials from Altair Material Data Center (AMDC)
In this release, polymeric materials can be imported from AMDC into the local material database of Inspire Extrude. AMDC has over 450 materials that can be used for polymer extrusion analysis. With a click of a button, the interface can connect to AMDC and users will be able to search the database and download what they need. (IEXT-2883)
The following issues have been resolved for the 2023 release:
General:
- Model Browser Part Icons. In this release, the model browser shows the icons of the imported part based on its type. For example, a part having only lines will have a line icon and a part with a volume not closed will indicate that in its icon, and so on. This will help the user to understand the imported model quickly. (IEXT-3083)
Metal Extrusion:
- Inconsistent Ram Speed Values in the Data Deck. The value of Ram Speed is specified in multiple places in the deck due to differences in the analysis types. There was an issue during multicycle analysis with different ram speeds and billet lengths for each cycle. The computed scaled variable step and change in billet length was leading to incorrect results. This issue is now addressed by internally making the ram speed consistent. (HXT-626)
- Error in Conform Extrusion Computation. For Conform Extrusion, there are two exits, one for the profile and the other to enable material leakage. The latter is for the material that doesn't go through the bearing. The Lagrangian data structure creation was failing for the leakage exit and more importantly, it is not needed there. This structure is used for the nose-cone analysis and is required only for the bearing and profile regions. Therefore, a check was added to avoid the creation of this data structure for the leakage exit surface. However, this fix will work only for standard meshes created by Inspire and will not work for all HEX meshes. (HXT-94)
- Dummy Block Position in Multicycle Analysis with Different Billet Lengths. The multi-cycle analysis supports the starter billet length option and the possibility to change the billet length from cycle to cycle. This feature is often used without the Dummy Block and works correctly. When the dummy block (tool) is included in the analysis, this tool component has to reposition itself to be in contact with the billet-dummy block contact surface. There was an issue with this feature and the dummy block was not repositioning. This issue is resolved now (HXT-13, HXT-163, HXT-676)
- Choke Projection. In the previous releases, bearing earing reference surfaces were meshed separately and they did not match the nodes/faces in the tool 3D mesh. Now, in order to improve the coupled analysis, the bearing reference surface mesh is now extracted from the tool side 3D mesh. This will enable the solver to easily determine the change in choke angle due to tool deformation. (IEXT-3105).
- Material Disappearance to Numerical Reasons in Charge Weld Computations. In the charge weld (also referred to as billet interface tracking and transverse weld) material was disappearing from the dead zones even after the exit had 100% new billet material. This was due to the numerical smoothing of the hyperbolic governing equation and this issue is resolved now (HXT-558)
Quenching
- Quenching Warpage Analysis. The warpage analysis in Quenching now shows results for all subcases in results explorer. In the previous releases, it was only showing two subcases, and this issue is now resolved. (IEXT-3164)
Polymer Extrusion:
- Flow Rate Conversion. The flow rate conversion was not unit consistent in the Inlet BC dialog. This issue is resolved in this release. (IEXT-3223)
- Use an Existing Mesh in Model Setup. The interface now allows using existing meshes in GRF format in the model setup. When this option is enabled, the interface will not generate a new mesh and use the specified existing mesh. (IEXT-3172)
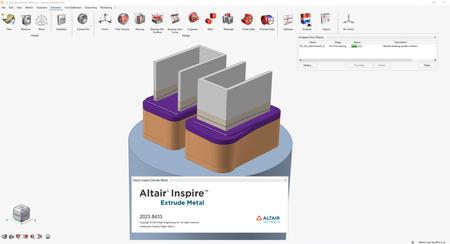
Altair Inspire Extrudeis a simulation environment designed to help extrusion companies meet the ever increasing demands to produce complex profiles with tight tolerances, quality surface finishes, and high strength properties at reduced cost. Altair Inspire Extrude is a simulation solution for both metal and polymer extrusion. It helps achieve productivity gains by reducing product development costs and improve extrusion quality, increasing production yield. Altair Inspire Extrude is a virtual press where users can visualize material flow and temperature inside a die during extrusion and make necessary changes to ensure balanced flow, while identifying and eliminating product defects.
Polymer Extrusion in Altair Inspire Extrude
Altairis a global technology company that provides software and cloud solutions in the areas of product development, high performance computing (HPC) and data analytics. Altair enables organizations across broad industry segments to compete more effectively in a connected world while creating a more sustainable future.

Rapidgator-->Click Link PeepLink Below Here Contains Rapidgator
http://peeplink.in/857a7d9f6952
NitroFlare
qxd9f.setup.rar
Uploadgig Free Links
qxd9f.setup.rar
Fikper Free Links
qxd9f.setup.rar.html
Links are Interchangeable - No Password - Single Extraction
