Altair Inspire Extrude 2024.1 Win x64
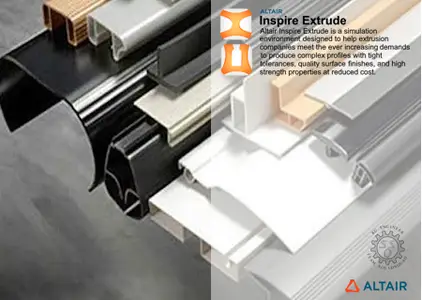
Free Download Altair Inspire Extrude 2024.1 | 4.9 Gb
Altairhas releasedInspire Extrude 2024.1is an easy-to-use tool for simulating metal extrusion, polymer extrusion, and friction stir welding processes to detect potential defects early in the product development phase and improve the process efficiency
Owner:Altair
Product Name:Inspire Extrude
Version:2024.1
Supported Architectures:x64
Website Home Page :www.altair.com
Languages Supported:english
System Requirements:Windows *
Size:4.9 Gb
New Features and Enhancements 2024.1
The Inspire Extrude 2024.1 release includes the following new features and enhancements.
General
Dynamic Legend
In this release, the dynamic legend is enabled for all results in the post-processing dialog. This feature can be turned on in the hamburger menu next to the legend in the dialog. Once enabled, when one goes through the result step-by-step, the bounds of the legend will be automatically updated as per the result of the selected step. (INSTRUDE-3623).
Metal Extrusion
Report Generation for Tool Deflection Analysis
In this release, report generation is supported for Tool Deflection Analysis. The report can be created after the tool deflection run is completed, and the result H3D file is available in the run folder. With a single click on the Report tool, it loads the results, orients the model automatically, positions the model in different views, and captures the images without user intervention. A PowerPoint document is created in the run folder with all the images and their corresponding legends. (INSTRUDE-3621)
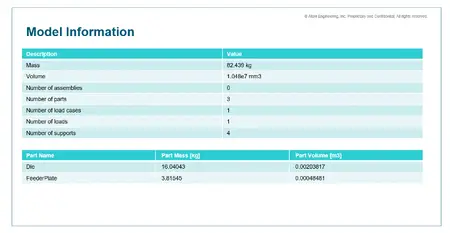
Transient Coupled Analysis with OptiStruct
In all previous releases, transient analysis was not supported by the coupled OptiStruct analysis. This combination is now supported. It is not necessary to compute tool stress analysis with OptiStruct every timestep the extrusion analysis is computed. The default value of this frequency parameter is 1 (compute every timestep). During the timestep when the tool stress analysis is performed, the solver automatically updates the temperature and loads using the extrusion results. This can be modified using the frequency parameter (TransientHXOSFrequency) in the Submit Run dialog. There is no change to the model setup workflow. Users can post-process both the extrusion and tool stress results by choosing them from the combo box. (INSTRUDE-3628)
Stationary Profile Analysis in Quenching
In this release, quenching analysis can be performed on a stationary profile. This is also a transient analysis, and the profile remains stationary. To enable this analysis, select the checkbox in the Export dialog and submit the run. (INSTRUDE-3627)
Automatic Transient Nose Cone Analysis
The transient nose cone analysis feature was available in the previous release, where the user had to manually set up the data in the TimeStep dialog. In this release, this step is simplified. In the Export dialog, the user can provide input for solely the Ram Acceleration Time and submit the run. In the background, the necessary timestep data will be generated and exported to the input files of the solver. (INSTRUDE-3629)
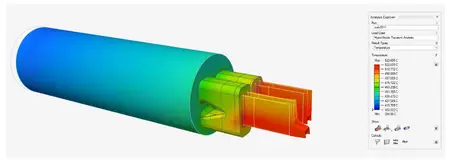
Mandrel Mesh Factor in Tool Deflection
In all previous releases, the mesh factor was enabled through a system environment variable. The user interface to enter this value was already enabled for coupled analysis in a previous release. This is now available in the Tool Deflection export dialog as well. Using this factor, the mesh on the load surfaces of Mandrel will be refined. (INSTRUDE-3456)
Renaming Bearing Start Curve
In Inspire Extrude, using the Bearing Start Curve tool, the user can extract the variable Bearing Start Curve. After extracting, the curve name doesn't follow the necessary convention. The user had to manually rename it according to its corresponding BearingCurve. There could often be mistakes in renaming the start curve. In this release, the user can right-click on the curve part and rename it as BearingStartCurve. Internally, the naming convention will be followed and the user need not worry about it. (INSTRUDE-3668)
Polymer Extrusion
Plate Die Creation
In this release, a plate die creation tool is implemented. This uses a semi-automatic process to create a plate die for a single polymer extrusion. The feature removes the barrier of requiring a CAD file of a die to start analysis. The user will start with the sketches (2D) of how the profile is generated from the inlet and create a lofted body using the Loft tool. The plate die will be created in a single click by selecting the plate cross-section (2D) and the lofted body. (INSTRUDE-3630)
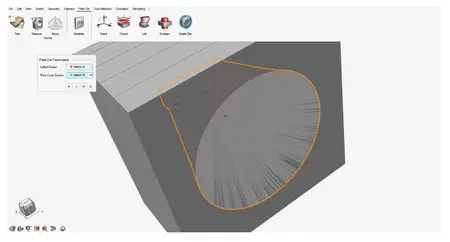
Report Generation for Tool Deflection Analysis
In this release, report generation is supported for Tool Deflection Analysis. The report can be created after the tool deflection run is completed, and the result H3D file is available in the run folder. With a single click on the Report tool, it loads the results, orients the model automatically, positions the model in different views, and captures the images without user intervention. A PPT document is created in the run folder with all the images and their corresponding legends. (INSTRUDE-3621)
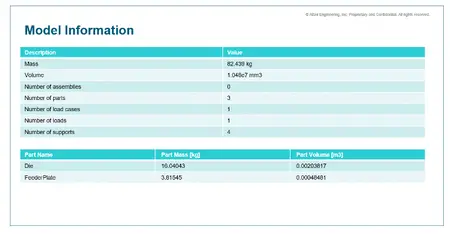
Resolved Issues
The following issues have been resolved for the 2024.1 release:
General:
- Number Precision Issues The numerical precision of values entered by users in some of the dialogs was reduced and made less precise due to rounding-off issues. This issue is resolved in this release. (INSTRUDE-3625)
HTC BC Creation:
- If the preferred language is not English, a crash was observed in the HTC BC context on selecting a surface. This issue is resolved in this release. (INSTRUDE-3646)
Quenching:
- Alloys need time-temperature-precipitation (TTP) curve data to perform quenching analysis. This data in the default alloy had inconsistent values and this issue is resolved in this release. In addition, TTP data was added for a few other alloys. (INSTRUDE-3679)
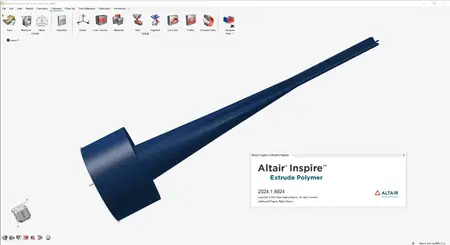
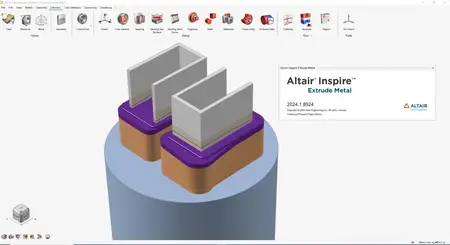
Altair Inspire Extrudeis a simulation environment designed to help extrusion companies meet the ever increasing demands to produce complex profiles with tight tolerances, quality surface finishes, and high strength properties at reduced cost. Altair Inspire Extrude is a simulation solution for both metal and polymer extrusion. It helps achieve productivity gains by reducing product development costs and improve extrusion quality, increasing production yield. Altair Inspire Extrude is a virtual press where users can visualize material flow and temperature inside a die during extrusion and make necessary changes to ensure balanced flow, while identifying and eliminating product defects.
Polymer Extrusion in Altair Inspire Extrude
Altairis a global technology company that provides software and cloud solutions in the areas of product development, high performance computing (HPC) and data analytics. Altair enables organizations across broad industry segments to compete more effectively in a connected world while creating a more sustainable future.
Rapidgator
http://peeplink.in/efbe118ba866
TakeFile
0xptz.Altair-Inspire-Extrude-2024-1.rar.html
Fikper Free Links
0xptz.Altair-Inspire-Extrude-2024-1.rar
Links are Interchangeable - No Password - Single Extraction
