Altair SimSolid 2024.1 Win x64
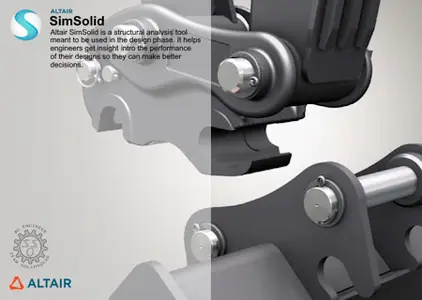
Free Download Altair SimSolid 2024.1 | 1.1 Gb
Altairhas releasedSimSolid 2024.1is a structural analysis software developed specifically for rapidly evolving design processes, enabling the analysis of fully-featured CAD assemblies in minutes without meshing
Owner:Altair
Product Name:SimSolid
Version:2024.1
Supported Architectures:x64
Website Home Page :www.altair.com
Languages Supported:english
System Requirements:Windows *
Size:1.1 Gb.
Altair SimSolid 2024.1 Release Notes
Response spectrum analysis
- Response spectrum analysis is a technique used to estimate the maximum response of a structure for a transient event. The time-history of the responses are not available. RSA is a simple and computationally inexpensive method to provide a peak response approximation, compared to conventional transient analysis.
- The solution is supported using four modal combination methods namely Absolute sum (ABS), Square root of sum of squares (SRSS), Navy research Laboratory's SRSS (NRL) and Complete quadratic combination (CQC). The solution requires linking to a modal analysis, which requires and uses most of the computational effort to obtain enough modes to represent the entire frequency range of input excitation and resulting response.
Collisions of deformed shape
- A new post processing capability is available for both structural and multi-loadcase analysis that finds possible collisions on all deformed parts in the assembly. The collisions can be found within a user-specified gap tolerance. The tool displays and lists all the possible collisions between all the deformed parts in the assembly.
Neuber stress
- Neuber stresses/strains can be obtained by running linear structural analysis and Neuber correction can be used to evaluate approximate local plasticity. This method is computationally inexpensive as Neuber stresses/strains are output without running a full-fledged nonline aranalysis. To successfully output Neuber results, material stress-strain curves are required to be input.
- The Neuber method corrects elastic results to capture any local plasticity. It is used to convert elastic stress/strain into real stress/strain when plastic deformation occurs. To apply Neuber's rule, compute stress (KtS) at a notch with elastic assumptions and when the stress exceeds the strength of the material, the real stress will show somewhere on the materials stress-strain curve at a point σ.
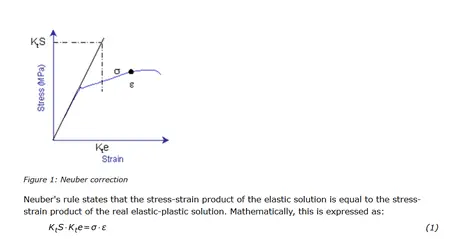
xAltair SimSolid 2024.1
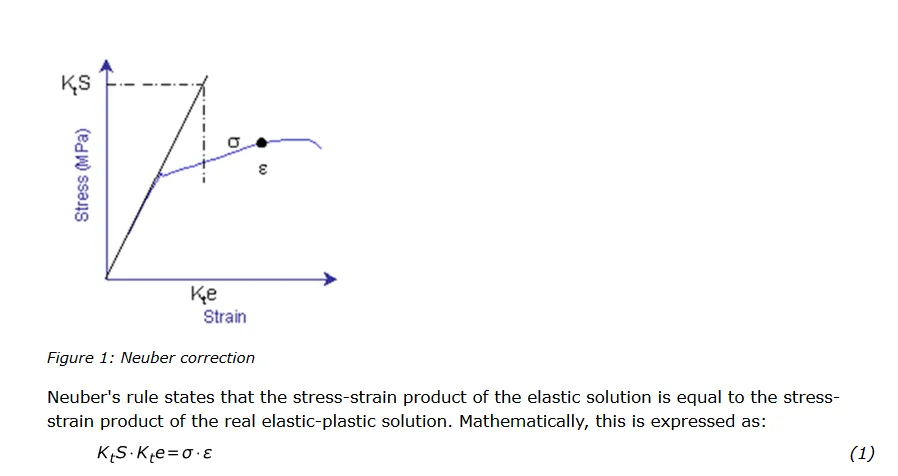
Close
Clamping contact condition
- A new contact condition called Clamping is now supported for structural analysis. The clamping contact condition allows parts to align in normal direction only, while allowing sliding between parts. Loads are applied internally to clamp the parts together. Graphics icon for clamping is a purple point cloud. The clamping condition is available only as a custom contact condition for structural analysis.
Trapezoidal seam welds
- The implicit seam welds created can now have a trapezoidal shape in addition to the existing prismatic shapes. This capability is available for both weld by lines/edges and weld from solids. These new welds can help in instances where creating prismatic shaped welds was difficult.
Multi-loadcases
- Several new boundary conditions are now supported under multi-loadcases including gravity, hydrostatic pressure, translational and rotational inertia, thermal loads, distributed mass and volumetric expansion/shrinkage.
- Result graph is supported.
- Export of deformed shape is supported.
Fatigue safety factor
- A new safety factor output is now available for fatigue analysis. Safety factor is available for fatigue via back-calculation to calculate scaling factor for a particular target life. It can be activated using fatigue solution settings.
Imported loads
Imported loads are now supported. Several loads can be imported from a CSV file including pressure for structural analysis and temperature, flux, convection for steady-state thermal analysis.
Composites (Beta)
- Orthotropic materials can be applied to plies within the laminates.
- Orthotropic material orientation can also be applied but it is limited to flat shapes. Separating/closing and Separating contact The contact conditions are now enhanced and made robust. The closing contact will work with gaps within the small-sliding zone. Any penetrations are automatically resolved when separating/ closing contact is used.
Others
- Part info is available for several parts in the assembly.
- ECAD files reader has been updated.
- Spot weld visualization has been improved where 2T, 3T, and 4T spot welds can be visualized in different colors. The 2T spot welds are highlighted in red, 3T in cyan, and 4T in pink.
- The adaptation for sheets has been improved which should resolve several numerical instabilities that yield error ID 18.
- Data imported from CSV files can now read more decimal places.
Known Issues
The following known issues will be addressed in a future release as we continuously improve performance of the software.
- Issues with linear guide joint under virtual connectors.
- Laminate creation and editing have been re-factored to improve the workflow.
- Issues related to updating the units appropriately.
- Issues related to result Descriptions have been resolved.
- Issues with importing fatigue material properties from a CSV file to material database.
- Issues related to re-using adaptation from previous steps leading to performance issues.
- Remote loads are updated appropriately when edited.
- Improved display issues with selection of parts.
- Improved creation of connections.
- Improved creation of seam welds.
- Status bar is updated appropriately when solution is being prepared before solving.
- Improved approximation of spots, when thermal loads are applied on spots.
- Result quantity labels are fixed when running dynamic analysis with displacement base excitation.
- Fixed issues and inconsistencies related to creation of virtual connectors.
- Issues related to dynamic reactions along bushing coordinate system
- Improved error messages.
- Inconsistencies with Descriptionting and saving results.
- Fixed issues related to boundary condition visualization.
- Boundary conditions can be applied to the face where distribution mass is applied.
- Issues related to handling boundary conditions appropriately in local studies.
- Issues related to complex eigenvalue analysis linked to geometric nonlinear analysis.
- Issues related to selection of material database.
- Issues related to assembly info with laminates.
- Issues related to bookmarks.
- Issues related to bolt forces.
- Several crashes have been fixed.
- Several instabilities have been resolved with improved adaptation.
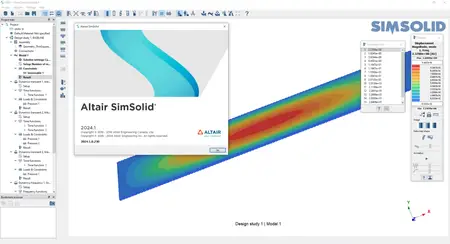
SimSolidis a game-changing simulation technology for designers and design engineers. Its just the perfect tool to kick-start any design process. This software completely eliminates the need for any geometry simplifications and meshing enabling you to get most out of your structural analysis in the least possible time. With SimSolid, model preparation is done within minutes. Even complex parts and large assemblies can be analysed with ease. SimSolid is tolerant of imprecise geometry and is just the right thing to accelerate your design process. In addition, this structural analysis solution is fast, really very fast. Highly accurate simulation results are obtained within minutes! Multiple design scenarios can be quickly analyzed and compared. And, accuracy can be specified on an individual part level allowing a rapid drill down to any level of detail that is required.
Introduction to Altair SimSolid
This video discusses some of the key benefits of Altair SimSolid and contains a detailed demo and product workflow. After viewing this video, you should be able to run your first simulation within the tool
Altairtransforms design and decision making by applying simulation, machine learning and optimization throughout product lifecycles. Our broad portfolio of simulation technology and patented units-based software licensing model enable Simulation-Driven Innovation for our customers. With more than 2,000 employees, Altair is headquartered in Troy, Michigan, USA and operates 71 offices throughout 24 countries. Altair serves more than 5,000 customers across broad industry segments.
Rapidgator
http://peeplink.in/3be444679447
TakeFile
wl0zu.Altair-SimSolid-2024-1.rar.html
Fikper Free Links
wl0zu.Altair-SimSolid-2024-1.rar
Links are Interchangeable - No Password - Single Extraction
